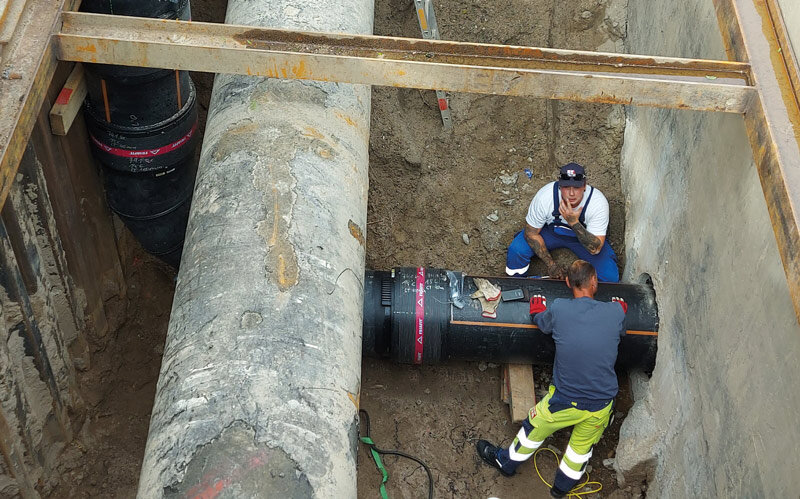
In Mannheim, the technology is state of the art. Today, 80% of the energy required is generated independently. The available regenerative resources such as solar energy or hydropower are used creatively for this purpose. Heat is also generated from wastewater and sewage sludge.
Urban drainage in Mannheim has a long tradition. Its beginnings go back to the 19th century. century. At that time, the dilapidated city ditch was laid up to six meters deep under the ring roads. The "Ringkanal" then functioned for many decades without any problems, and a high level of technical expertise was involved right from the start, with renowned wastewater experts such as Mannheim-born Dr. Karl Imhoff (1876-1965) and William H. Lindley (1853-1917) making valuable contributions. For many generations up to the present day, the pioneering spirit and willingness to innovate, coupled with ecological awareness, have determined the thinking of those responsible. Since July 2016, EBS has been operating Europe's first large-scale plant to remove trace substances from wastewater using the 4th purification stage.
The centerpiece is the powdered activated carbon (PAC) plant
The purpose of this adsorption stage is to significantly reduce the load of trace substances: pharmaceutical residues (hormones, painkillers, antibiotics, etc.) or chemical substances such as anti-corrosion agents are filtered out before being discharged into the "receiving water", the Rhine. The PAH ensures that around 90% of the wastewater is treated and 80% of these trace substances are eliminated. When it rains heavily, the plant's capacity is exceeded and the remaining 10% is discharged directly into the receiving waters in a highly diluted state.
Corrosion leads to leaks
The PAH must function reliably and trouble-free. An important part of the filter system is a pressure pipe that feeds the treated wastewater back into the treatment circuit via the primary clarifier. This steel pipe was around five meters deep and was permanently "soaked" due to strongly changing groundwater levels. This damaged the steel and caused pitting.
The solution: polyethylene (PE)
A modern solution was also chosen for the repair at this point, replacing the steel pipe material with PE. The smooth surface prevents water from penetrating. Corrosion is therefore unknown in connection with PE, and the measure was planned in accordance with the existing conditions and implemented quickly.
The Aliaxis Germany factory
Essentially, two pipe layers were prefabricated at the factory and then professionally installed on the construction site with other components by SAX + KLEE, which supplies a wide range of customized solutions in manufacturer quality - pipe components, distributors, branches and shafts - always with a perfect fit. In the end, both the construction company and the client benefit, as valuable construction time is saved and downtimes in the construction process can be reduced.